How Processes and Accountability Translate to Performance
In an initiative to increase the reliability of their electric system serving roughly 11 million Florida residents, Florida Power & Light (FPL) set out to replace more than 3,700 aging H-frame 500kV structures. In 2017, the utility released more than 1,000 miles of 500kV transmission rebuild projects in a unique, phased approach. Unique, because initial phases would award EPC (Engineer, Procure, Construct) foundation contracts, to be followed up with structure placement at a later date. Foundations would therefore need to be installed under existing energized 500kV transmission lines adding an additional layer of complexity to the scope. Traditional approaches typically see structures set in the same phase as foundation construction, but this approach was selected, in part, as it allowed for increased outage flexibility and a reduced overall impact on FPL’s customer base.
Irby Construction Company (Irby), in partnership with Crux Subsurface (Crux), was quick to bid. The team set its sights on securing multiple phases of work from each RFP released in the hopes of furthering an already longstanding relationship and track record of success with FPL. Irby’s team was ultimately awarded one of the first phases of the FPL 500kV EPC Foundation Projects; Phase B. Phase B was the first of several phases, and it was almost the last for Irby. The team quickly found itself in trouble over quality issues–losing time, money, and FPL’s trust. Feeling defeated but committed to performing, Irby’s team pulled together and developed a comprehensive Quality Management Plan (QMP) intended to reset and revolutionize their approach.
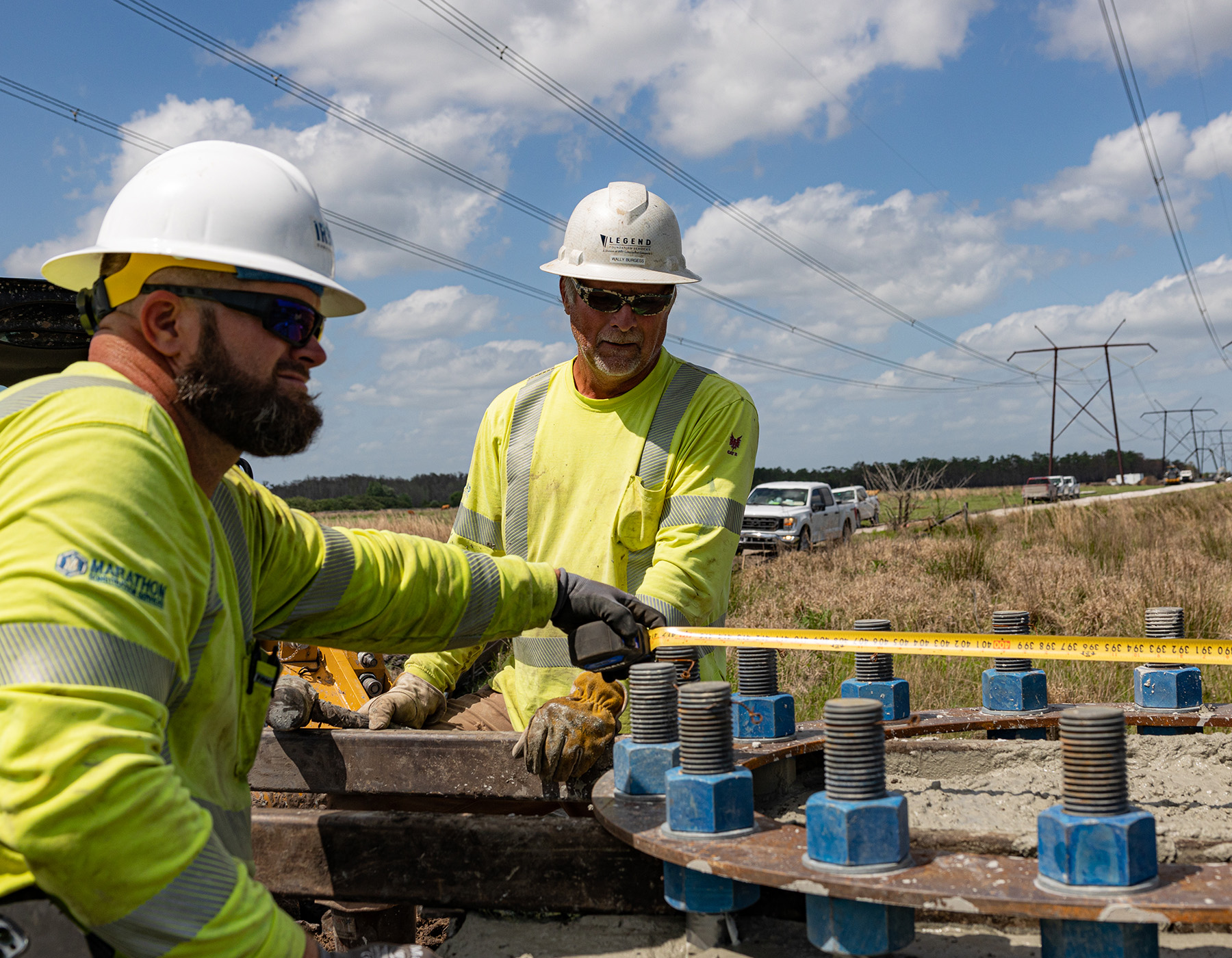
How it Started – Phase B
Terrytown to Orange River Substation, known as Phase B, involved the replacement of 260 structures, resulting in the design and construction of 520 drilled shaft foundations across the 70-mile alignment. The scope of work was primarily conventional land-based drilling but also included a number of challenging locations in marsh-like conditions, requiring advanced expertise and specialty equipment.
At the onset, the Irby team seemed to have all the right components: a proven track record with the client; substantial experience in the area; and a strong team of foundation partners, including Crux, Marathon Construction Services, MJ Drilling, and Aldridge Electric. However, challenges quickly surfaced. FPL’s design specifications were straightforward, and Crux’s Issued for Construction (IFC) drawings complied with these specifications, but the team encountered difficulties verifying the specifications in the field.
Irby’s typical contracting method involves foundation construction and structure-setting in the same scope of work. This approach effectively puts the responsibility on the prime contractor to ensure installed foundation tolerances can accommodate the structures. And, in the event connections don’t line up, the problems surface quickly as the structures are set shortly behind foundation completion. Though FPL’s phased approach has the potential to minimize outages and substantially reduce overall project costs, it created quality challenges the foundation team was not accustomed to. In the absence of prompt structure setting to confirm foundation tolerances, the installing contractors were tasked with taking Quality Assurance (QA) measurements upon completion. FPL’s QA inspector followed by taking their own measurements for verification. This verification process saw an unacceptably high number of sites flagged with engineering issues; a small handful of which truly did fall outside allowable tolerances, but also a substantial number which were in compliance and showed discrepancies due to data collection inconsistencies. It became apparent that consistent standards had not been established for measurement collection and reporting across the Irby team and with FPL. Minute differences in processes were delivering measurable data variances that often specified rework to correct–sometimes unnecessarily.
As Phase B progressed, Irby found itself backtracking, losing ground, and failing to perform according to planned schedule. Costs and frustrations were mounting on all sides, and team leaders were looking for answers as they fell further behind schedule. Ultimately, Irby delivered Phase B to FPL behind schedule and with costs exceeding projections. It was recognized that if Irby wanted to continue pursuing future phases of this work, dramatic changes would need to be quickly implemented and executed.
The Pivot Point – Establishing a Quality Program
After the rocky conclusion of Phase B, the Irby team was at a critical juncture with FPL. They wanted to pursue additional phases of work but concluded that major changes would need to be made. The team recognized that the missing component was a comprehensive Quality Management Plan (QMP) and began working to establish one.
The starting point was a version of the QMP Crux had developed for a major fire-hardening effort in Southern California. The project also had multiple phases and coordinated several contracting entities, imposing a number of the same challenges experienced in Phase B. The Plan was then customized to meet the needs of the FPL projects and address three core objectives: to define, improve, and control processes to align with FPL’s needs and expectations as expressed in the contract documents.
One of the first steps was to differentiate between Quality Assurance (QA) and Quality Control (QC). Too often in this industry we say “QA/QC,” effectively lumping together two distinctly different disciplines together into a single term. The process of developing the FPL-specific QMP began by talking about these differences and distinguishing the engineering accountability around QA from the construction accountability around QC. Once this distinction became clear, the team was able to better evaluate the specific functions for each effort and, more importantly, the person or people responsible for each specific function. The team adopted and kept at the forefront of their planning process the definitions for these two concepts as defined by ISO 9000: 2015 Quality Management Systems:
- Quality Assurance is the part of quality management that focuses on providing confidence that quality requirements will be fulfilled or all the planned and systematic activities implemented within the quality system can be demonstrated to provide confidence that the product or service will fulfill the requirements of quality.
- Quality Control is the part of quality management focused on fulfilling quality requirements or the operational techniques and activities used to fulfill requirements for quality.
Effective documentation would supplement the QMP by preventing mistakes and avoiding rework/delays during construction through early detection. The final QMP clearly defined roles and responsibilities and outlined these in a standard Inspection and Test Plan (ITP). The ITP would be used to communicate the responsibility level of each role assigned to the project, provide a step-by-step outline and include the testing and/or inspection required at each step; and detail which form should be used to document the completion of each step.
The result of these in-depth discussions and brainstorming sessions was a comprehensive QMP the team felt was ready to present to FPL and roll out in the field.
Creating Confidence & Reestablishing Trust
Prior to the award of the next phase, the team made what felt like a “Hail Mary” attempt to assure FPL they were capable of successfully completing future work.
In an in-person presentation to FPL, the Irby team walked through the details of the plan. They demonstrated that accountability wasn’t merely established, but that names were assigned to each individual function. This included the development of new positions when needed to support the QMP and ensure proper implementation. The presentation detailed scope and activities for QA and QC separately; documentation and monitoring procedures were reviewed; training material to be distributed to operations crews was presented; consistent installation practices between multiple contractors were outlined; and required documentation for foundation closeout was covered in detail.
The team also presented the portion of the QMP which focused on proactive, ongoing training to keep quality at the forefront. A review of quality lessons learned from Phase B revealed that the majority of foundations experiencing verified quality issues occurred within the first few weeks of a new foundation crew starting on the project. To mitigate these occurrences, the developed QMP places substantial emphasis on properly training crews in these first few weeks. Quality Refresher Courses would be presented each time a new crew begins work, including mock measurement practice and a thorough review of all aspects of project specifications and the QMP. The invitation to attend these courses would extend beyond new crew members to all stakeholders, including FPL employees. Hard hat stickers would be provided to everyone who completes the course for easy identification in the field. The underlying concept of this type of training is to promote continual learning and enhanced communication around quality, promoting regular discussion and improvement throughout the lifecycle of the project.
The ensuing presentation discussion provided FPL the opportunity to ask questions and voice concerns; all of which the Irby team had responses for. Ultimately, FPL determined the Irby team was capable of tackling subsequent phases and Phase I was awarded.
Implementation and the Addition of ProTRAQ™
The team knew successful implementation of the developed QMP would require sophisticated project tracking, data collection, and reporting. They were going to need a streamlined approach to facilitate implementation and a digital application was the obvious answer. Crux was already using ArcGIS – an interactive mapping software – to build a comprehensive geotechnical database, and the team determined there was potential to adapt the software and create a more comprehensive program management tool. The team then began additional development specific to the FPL projects and the implementation of the QMP.
The resulting ProTRAQ™ application was a fully customizable program management tool that digitalized forms with built-in QC capabilities based on spec requirements detailed in the QMP. The system provides real-time snapshots of project progress to stakeholders in the form of maps and project dashboards. In addition, tracking spreadsheets and reports are generated daily to monitor activity and completion milestones.
ProTRAQ™ puts iPads in the hands of QA and QC field personnel, providing an efficient avenue for required documentation to be uploaded and giving key, often remote, stakeholders real-time updates and visibility into project progress. The application is also designed to automatically identify entries outside design and specification requirements, notifying the user upon upload and allowing for issues to be addressed in a timely manner.
Going in Better Prepared - Phase I
Gaco Substation to Roberts Substation, known as Phase I, included 419 structure replacements, entailing the design and installation of 838 drilled shaft foundations across the 58-mile alignment. The scope mirrored Phase B, but construction operations were substantially smoother, driven by the collaborative QMP implemented using ProTRAQ™. Explicitly defining the QA and QC steps to be used in construction – inclusive of monitoring actions, reporting mechanisms, and documentation formats – proved highly valuable. It established how construction monitoring QC should be performed and how modifications to construction procedures should be implemented in response to the monitoring actions. Further, it described QA methods and protocols for project personnel to ensure a complete understanding of the quality system.
Report submissions are one area where increased efficiencies have been especially clear. The table above illustrates the difference in submittal times for Owner required closeout documentation between Phase B and Phase I. The average time dropped drastically between the two phases, from 146 days to 42 days. Reducing the time required to complete closeout documentation subsequently allows for final invoicing and release of retainage to occur much earlier.
The Irby team concluded Phase I ahead of schedule and with costs aligned to project estimates. FPL noted the significant quality improvements and subsequent positive impact they had on both production rates and overall project safety. The results of the QMP exceeded even the team’s own expectations, and various aspects have been adopted by Irby and other team members across unrelated scopes of work.
How It’s Going – Phase C and Beyond
Since Phase I, the Irby team successfully completed Phase C, with a scope of 342 drilled shaft foundations, and is currently installing a total 1,678 drilled shaft foundations between Phases E, F, and G. The team is also preparing to begin work on the next Phase and hopes to have installed more than 3,300 total foundations between all phases of work by the end of November 2023. Additional foundation partners have been brought in to enhance the team, including Legend Foundation Services and RR Cassidy, and the group continues to strive for increased efficiencies to deliver successful projects.
The multiple phases of FPL’s 500kV EPC Foundation Projects clearly demonstrate the benefits that a comprehensive and well-implemented QMP can provide to a project of this nature. They serve as an excellent example of a team stepping back to assess an approach that clearly wasn’t working, and collaborating to develop a solution that fit the needs of the project. What could have been chalked up to a loss and lesson learned was translated into a success and continued future collaboration with FPL through an intense dedication to continuing Irby’s promise of “Absolute Performance” for its customers.
ANDRE FOSTER, IRBY CONSTRUCTION COMPANY, SYDNEY MCNEAL, CRUX SUBSURFACE
Published By: Irby Construction Company Feature, Foundation Drilling | May/June 2022