PAR Electrical Contractors demonstrates unigue work methods as it installs structures on SDG&E’s recently energized line.
A new 117-mile transmission line now winds through a national forest, traverses an arid desert and climbs through the mountains of California from Imperial County to San Diego County.
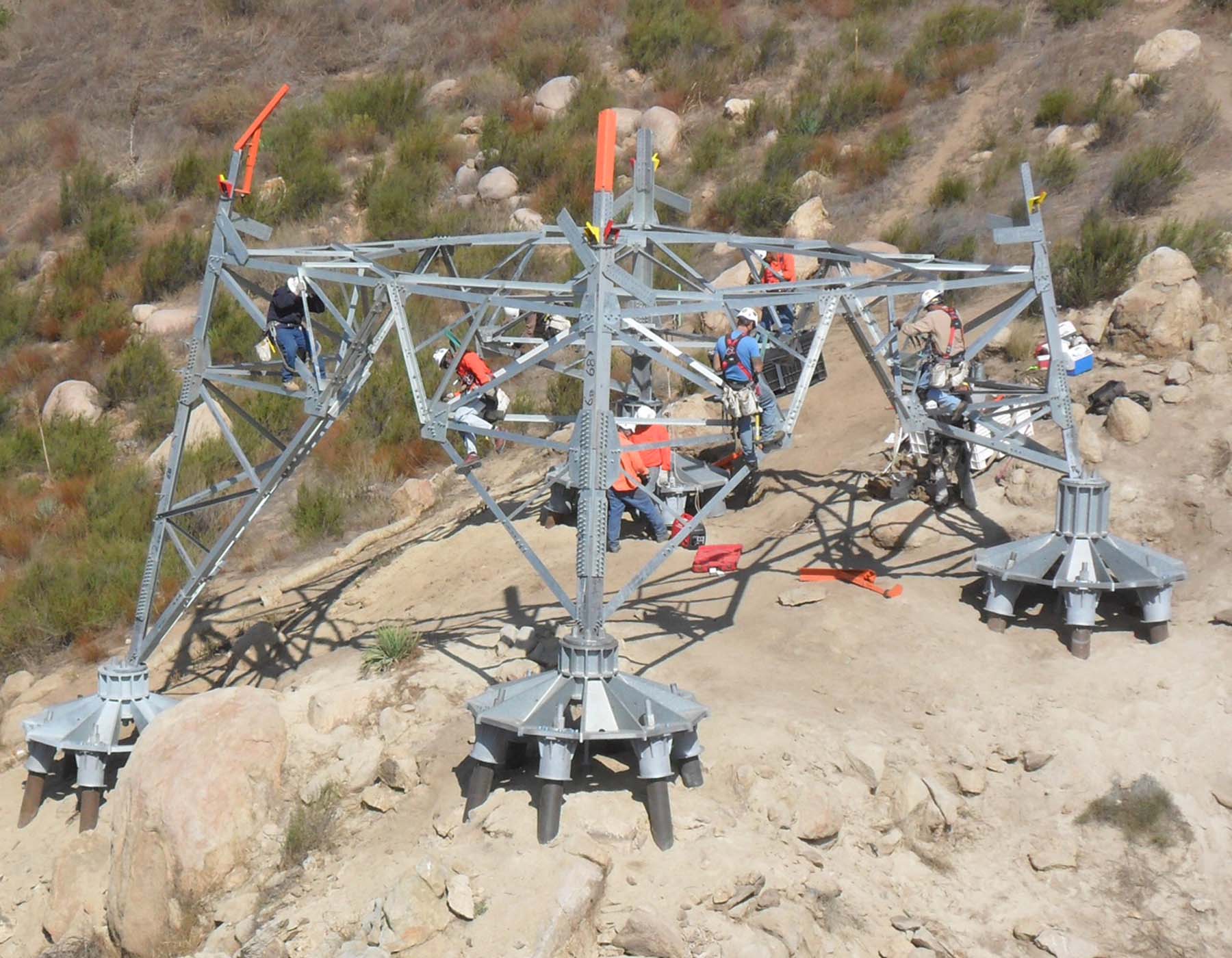
Inspection of steel cap prior to stub angle setting in Mountain Springs Grade area.
Companies Mentioned
American Eurocopter
Bell Helicopter Textron
Beta Engineering
Bobcat Co.
Crux Subsurface Inc.
Erickson Air-Crane
Kaman
PAR Electrical Contractors Inc.
San Diego Gas & Electric
Overview
Called the Sunrise Powerlink, the recently energized line is comprised of two 230-kV segments (one overhead and one underground), a 500-kV segment and a new 500-kV/230-kV transmission substation called Suncrest substation.
The San Diego Gas & Electric (SDG&E) project team and its prime contractor, PAR Electrical Contractors, spent 18 months constructing the line, which connects two existing substations, SDG&E's Imperial Valley substation near El Centro California, and SDG&E's Sycamore substation just north of the city of San Diego. Sunrise Powerlink is designed to deliver up to 1,000 MW of planned renewable energy to San Diego while greatly increasing the transmission import capability.
The nearly $1.9 billion project begins at the desert floor at sea level and then rises up as high as 5,600 ft in the forest. It then drops back down to less than 1,000 ft above sea level at the Sycamore substation. One of the spans on the 500-kV line is almost 5,200 ft long. Dubbed the "Mile Span," it is now the longest span in SDG&E's system. The Sunrise Powerlink also crosses Interstate 8 five different times and shifts from overhead to underground for 6 miles in Alpine, California. The other 111 miles are a combination of 230-kV and 500-kV overhead transmission lines, with more than half of the line crossing through rugged terrain made accessible only with helicopters.
The San Diego Gas & Electric (SDG&E) project team and its prime contractor, PAR Electrical Contractors, spent 18 months constructing the line, which connects two existing substations, SDG&E's Imperial Valley substation near El Centro California, and SDG&E's Sycamore substation just north of the city of San Diego.
Protecting Wildlife and the Environment
Crews constructed this line in a serpentine-like path to accommodate the hundreds of environmental and vegetation management mitigation measures. For example, the line crosses through habitat for the endangered Peninsular Big Horn Sheep, a boulder-strewn landscape where the construction window was limited to only six months so as to avoid construction during the lambing period in this area.
Due to the limited construction windows, much of the conductor installation was pursued quickly. For example, workers had to complete the almost mile-long span within a three-week period in an area designated as a Golden Eagle habitat. Similar construction window closings threatened the conductor installation completions in four other areas. In addition, the environmental restrictions didn't permit the inclusion of a snub site in the Mountain Springs Grade area. In this moonscape-like rugged habitat, the crews installed a set of explosive-type conductor sleeves for a conductor pull. Environmental restrictions prohibited SDG&E from building roads to 234 of its 421 lattice steel towers. As a result, the utility used helicopters to construct these towers from start to finish. As many as 35 helicopters worked on the project on a single day. More than 30,000 flight hours were logged by a combination of passenger, medium and heavy lift helicopters. Helicopter types used on Sunrise included Erickson Skycranes S64 E and F models, Bell 205 and 212 models, Kaman K-MAX, Eurocopter AS350 B2 and B3 models, the MD500, the MD520 NOTAR and MD530F. Faced with the heavy lift construction requirements at more than half of the structure sites, SDG&E purchased an Erickson F Model Skycrane (the "Sunbird") for dedicated use on Sunrise. At various times during the project construction, the company brought in additional F and E model Erickson Skycranes to assist.
As many as 35 helicopters worked on the project on a single day. More than 30,000 flight hours were logged by a combination of passenger, medium and heavy lift helicopters.
Preparing the Work Site
SDG&E required all project personnel to be trained on environmental mitigation measures, wildfire suppression requirements and helicopter safety. This training pertained not only to the crews who built the line, but also construction and quality-control support personnel, inspectors responsible for the inspection of the contractor's work and environmental monitors required by the mitigation measures to be on site during construction activities. Everyone was trained in how to safely use the helicopter landing pads at the remote structure sites. Crews also were trained in hot load/unload techniques, which refer to loading and unloading personnel on the helicopter without shutting down the engine. Many landing sites were not on level ground, which added to the risk of injury during this process.
At the remote sites, the contractors had to perform all tasks including vegetation clearing, foundation installation, steel erection and wire stringing via the air rather than from roads on the ground. The first step for the field crews was to clear a landing zone for the helicopters. By removing the vegetation in a 70-ft diameter landing zone, the work crews could load and unload from the helicopter safely with a reduced risk of fire.
To help the vegetation management crews to clear the brush and trees, the heavy lift helicopter pilot flew in equipment like a Bobcat and/or small hand tools such as shovels, rakes, chain saws, axes, brush cutters and firefighting equipment. Next, the vegetation management team cleared a 100-ft by 100-ft footprint for the tower construction. The helicopter then hauled out the vegetation since it couldn't be spread out on the site.
Constructing Foundations
Once the tower sites were cleared of vegetation, the crews prepared the site for the construction of the foundations. Somewhat less than half of the foundations were conventionally constructed with augers, rock hammers, blasting, and other conventional means and methods employed at sites with vehicle access. Batch plants delivered concrete for the minority of the sites, and specialized trucks mixed volumetric concrete at most of the conventional sites.
At the remote sites, PAR and its subcontractor, Crux Subsurface Inc., proposed and ultimately employed a design-build micropile foundation system as an alternate to traditional concrete drilled shaft foundations. Many of the tower sites feature boulder-covered terrain and/or near surface hard rock out- · crops. The use of the micropile foundations eliminated the need to blast IO-ft-diameter holes 20 ft to 30 ft deep into the mostly rocky strata. Instead, the workers installed an array of three to a dozen 8-inch-diameter micropiles to a typical depth of 35 ft at each tower leg.
To begin construction of these foundations, the crews removed large boulders and benched the area where the workers would construct the four tower legs. The helicopter then brought in specialized equipment beginning with a platform and a lightweight specialized drilling rig. The adjustable leg platform and the drill rig separated into several pieces to facilitate the transport with medium lift helicopters, allowing loads to be safely managed by ground crews on steep terrain. The medium lift helicopter then transported the drill as well as an air compressor, generator, steel casings, threaded rods and small tools to the site. The proprietary drill rig rotates about a centroid to efficiently install each micropile with enough precision to facilitate bolted connections between the micropiles and pile caps. Once a group of micropiles is installed, the helicopter moves the drill rig and platform to the next leg location.
The sequence of micropile installation in rock included placement of an upper steel casing to a prescribed depth followed by drilling and placement of high-strength all-thread rebar into the lower bond zone, extending the full length of the pile. Each pile was grouted with high-strength cementious grout from the bottom to the top. Where foundations were installed in soil, pressure was applied to the grout while casings were retracted from the bonded section. A minimum of two piles were proof tested at each tower. Crews tested the piles to their maximum factored load.
After proof testing and trimming of the casings, the next step was to install a cap on the micropile casings. In a departure from conventional tower foundations with concrete caps, SDG&E worked with its contractors to develop a unique steel pile cap for use on the Sunrise transmission towers. SDG&E previously had approved the use of steel pile caps on tubular steel poles, but never before on a lattice steel tower. Given SDG&E's previous success with steel pile caps on monopoles, the utility and its contractors decided to consider using a steel cap for the Sunrise towers, as well. SDG&E's engineers agreed it would make more sense to use a steel cap, rather than a concrete cap, providing that the performance of the steel cap was equal to or better than a concrete cap. As a result, the Sunrise Powerlink project is the first application of steel cap micropile foundations for lattice steel towers in the nation.
The use of steel pile caps eliminated the need to transport and form rebar cages, fly in forms and several yards of concrete to the remote work sites, and then pour concrete around the micropile foundation to form the pile caps. It also reduced helicopter emissions. Each steel pile cap weighs 5,000 lb, and a medium lift helicopter only needs to make four trips to transport the four caps needed for each structure. In comparison, medium lift helicopters would need to make 40 to 50 flights to fly 130,000 lb of concrete to a site, and when multiplied by 234 sites, it adds up to a significant savings in environmental impact and construction time. Once the crews installed the steel pile caps, and the stub angles were grouted in place, the foundation was complete and ready for the tower steel.
Erecting the Towers
Environmental restrictions created some unique challenges on the Sunrise project when it came to erecting the starter legs for the steel towers. Traditionally, the crews need to install guy wire to tie back each leg, temporarily supporting it until all four legs can be bolted together.
During this process, a helicopter flies a leg to the site, and workers guide it into place on the stub angle and attach the temporary guy wire. They would then successively set each leg in place with temporary guy wires. Once the crew members set the connecting steel members into place to tie the legs together, they could remove the temporary guys. Due to Sunrise's environmental mitigation measures, the crews were not always permitted to install the guy wires and extend them outside the 100-ft by 100-ft tower footprint. The problem the construction team faced, however, is that not all the legs can be supported by guys remaining within the tower footprint. To address this challenge, SDG&E's contractor developed unique braces for the legs that work as kickstands to temporarily support the legs. A helicopter flew in each leg as a stable unit, and it supported itself until it was connected to the other legs. Once all four legs were installed and tied together, the remaining sections of the tower were brought in by the heavy lift helicopter.
To facilitate the flights, SDG&E set up staging yards about every 5 miles to 7 miles along the project alignment. These yards varied in size, some exceeding 30 acres. The yards served as sites where crews could preassemble the tower sections and prepare them for transport via helicopter. Once the helicopter picked up the preassembled tower sections, the crews could then stack the sections, one after the other. After the starter legs, crews added the body extension(s), followed by the Y.. shaped layback and finally the bridge. The completed heavy dead end bridges were too heavy for the helicopter to lift, so the crews split them into two pieces. Conventional means and methods for split bridge erection uses a system of guy wires. Workers are often positioned under the tower to secure these wires on temporary anchors as the helicopter sets each half bridge on the tower. Because Sunrise has so many remotely sited heavy dead end towers, this raised a safety concern for a significant amount of exposure. The workers had to be below the tower when the helicopter set the half bridge sections on the tower.
In a successful effort to reduce the risks associated with the setting of the split bridges, SDG&E worked with the Sunrise contractor and consulting engineers to design unique internal bracing that could be attached temporarily to each of the split bridge sections. Using this bracing, the helicopter sets each half bridge section on to the tower as a stable unit where it temporarily supports itself until the other half bridge is flown into place. Finally, both half bridges are securely tied together to form the completed bridge assembly.
Once the towers were complete, the conductors and shield wires were installed. The workers used a unique netting installation over the five CALTRANS crossings of lnterstate 8 so conductor pulling could take place without workday or traffic restrictions. The supporting poles and guy wires for the nets were erected in the CALTRANS right-of-way during Sunday morning periods of light traffic and with a few brief traffic closures. The nets and the supporting guy wires were pulled across the right-of-way in just a few minutes, minimizing the traffic disruption. Additionally the two OPGW shield wires on the 500-kV line and the single OPGW shield wire on the 230-kV line each contained 72 optical fibers, sometimes requiring specific stringing sites and always requiring additional attention for successful splicing at both accessible and inaccessible locations.
After the completion of the conductor installations, the crews completed the aircraft warning light installations. Two different kinds of lights - visible and infrared - were used on Sunrise. The visible lights were installed in accordance with the results of an aeronautical study and in compliance withFAA regulations. The visible lights themselves are not unusual except that they are all solar powered because of the remote locations. Additionally SDG&E worked with military and law enforcement agencies in San Diego and Imperial counties to identify locations where solar-powered infrared lighting would enhance pilot safety. The infrared lights can only be seen with specialized infrared goggles. These lights are. clearly visible to the pilots from agencies that often fly at night in remote areas near the Sunrise alignment.
Working with a new low-power supervisory control and data acquisition (SCADA) system supplier, SDG&E installed a SCADA system to continuously monitor the status of the visible and infrared lights. Should there be a problem with the lights, an alarm would be triggered and a maintenance crew dispatched to make necessary repairs. This system eliminates the need for field workers to expend time and effort to inspect all 117 miles of the transmission line for aircraft warning light outages. Instead, the SCADA system automatically monitors the condition of the tower lighting systems.
While the transmission line was under construction, Beta Engineering, SDG&E's prime contractor for the Suncrest substation, completed the construction of the 500-kV/230-kV transmission substation. Starting with a greenfield site, the workers excavated, crushed and re-compacted 1.2 million cubic yards of soil and rock to create the pad at this balanced site. Working under a compressed construction schedule, all the below-grade and above-grade work was completed in just 16 months.
After 18 months spent in the desert and the mountains to construct the Sunrise Powerlink, SDG&E recently celebrated the energizing of the line. SDG&E and its contractors compiled an exceptional safety record by working more than 5 million man-hours without a major incident. The OSHA incident rate of 1.81 was less than half of the industry average of 3.80 for similar utility projects, despite the heavy reliance on helicopters and construction in rugged terrain. The Sunrise Powerlink was anything but a typical utility project. The attention to safety was greatly enhanced by the full-time operation of the Sunrise Base - a communications center that maintained constant contact and knowledge of whereabouts of all field personnel, helicopters, and unique risks and concerns associated with specific locations. Now that the Sunrise Powerlink project is operational, and once the renewable energy projects in Imperial and San Diego counties are brought on-line, Sunrise will carry clean, green electricity to the residents of San Diego. In addition, SDG&E and its ratepayers will benefit from the use of the innovative Sunrise techniques and work methods that also may be applied to future projects.
Reprinted with permission from August 1, 2012. Transmission & Distribution World, Penton Media, Inc. Copyright 2012. All rights reserved. For more information on the use of this content, contact Wright's Media at 877-652-5295 DOWNLOAD